Operational Excellence Specialist
Posted on Jan. 11, 2025 by Amgen
- Dún Laoghaire, Ireland
- N/A
- nan
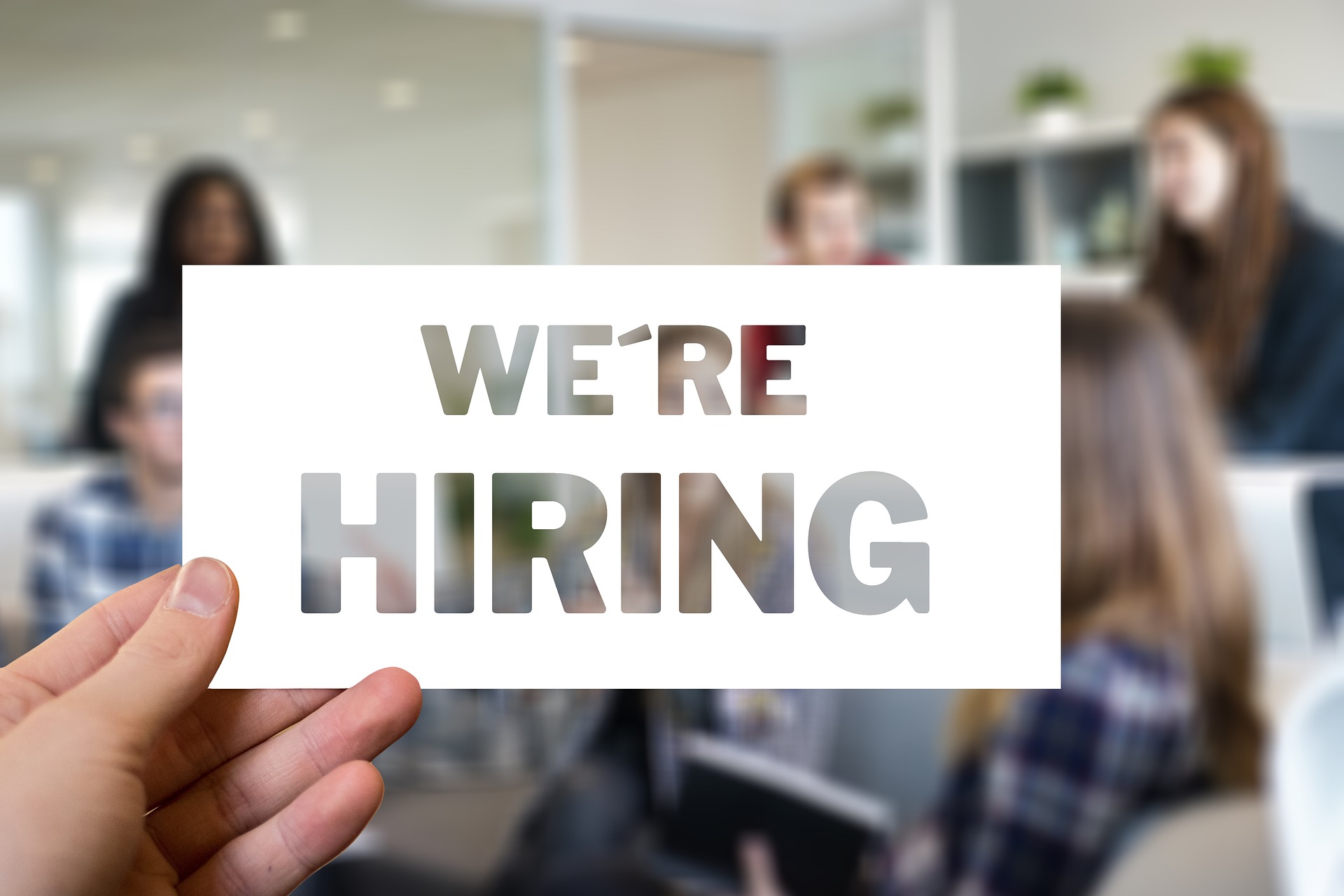
This role is a key member of the Site Operational Excellence Group, reporting to the Senior Manager of Operational Excellence. The mandate of this group is to enable teams and business functions to improve operations and reduce waste by enhancing reliability and efficiency through the application of Continuous Improvement tools, techniques, and methodologies. The OE Specialist will measure performance and find opportunities to optimize and improve productivity. This role requires in-depth knowledge of continuous improvement tools, techniques, and methodologies, along with practical experience in applying them to improve the performance of processes, equipment, people, and systems. The Industrial Engineer will engage with internal customers to support their efforts in solving complex problems and improving performance.
Key Responsibilities:
- Perform analysis and diagnostics to identify opportunities for improvement and make recommendations to leadership.
- Coordinate idea generation, project identification, prioritization, and overall selection, ensuring that projects are integrated with business strategies.
- Support the design and delivery of Lean/Six Sigma projects as part of a cross-functional team.
- Identify and justify project financial savings.
- Support teams assigned to implementing the recommendations.
- Design and facilitate workshops and Kaizen events.
- Drive achievement for own projects and projects they are supporting.
- Develop standards (labor/machine) and resource modeling.
- Train all levels of the organization on OE principles and methodologies through our OE Training Program.
- Coach and mentor Project Sponsors, Black Belts/Green Belts candidates on the proper use of tools, improvement processes, and deployment issues.
- Encourage an OE culture by influencing and empowering employees to see opportunities to apply techniques and tools in everyday work activities.
- Facilitate the sharing of best practices and project successes across the organization.
- Facilitate communications and change management for key programs and projects.
- Act as the process owner for a lean practice, responsible for the deployment approach.
- Perform any other tasks/projects assigned by the manager.
Basic Qualifications & Experience:
- Bachelor’s degree in a scientific or engineering subject area plus a minimum of 3-5 years of relevant experience.
- Experience in Project Management.
- Experience in manufacturing, technology, and supply chain, with experience in Drug Product manufacturing considered an advantage.
- Knowledge and understanding of manufacturing processes, cGMP, industry regulations, product development, and commercialization.
- In-depth knowledge of at least one structured problem-solving approach (e.g., A3, DMAIC, 8D, etc.).
Preferred Qualifications & Experience:
- Lean Six Sigma Green Belt or equivalent.
Competencies / Skills:
- Exceptional data analysis skills, including acquisition and presentation of data. Proficiency in at least one of the following: Microsoft PowerQuery, Spotfire, developing SQL queries for data analysis.
- Ability to successfully operate in a matrix or team environment with site, divisional, and corporate executive leadership.
- Ability to manage multiple responsibilities, priorities, and tasks with minimal direction.
- Excellent oral and written communication skills.
- Excellent interpersonal skills to drive change management and influence for improvement.
- Strong capabilities with Microsoft Office and Power Platform software – Power BI, Excel, PowerQuery, Project for the Web, PowerAutomate, as well as Word, PowerPoint, etc.
- Experience implementing Continuous Improvement methodologies such as Six Sigma, DMAIC, and/or Lean Manufacturing.
- Experience developing standards (labor/machine) and performing resource modeling.
- Experience with regulated environments (i.e., cGMP, OSHA, EPA).
- Exceptional capacity to analyze facts and develop logical conclusions.
- Strong observational and listening skills – capable of quickly understanding the core elements of a new process.
- Excellent process mapping capabilities – capable of independently mapping a process and leading a team to map a process in a workshop event.
- Digital skills – comfortable acting as a power user and early adopter of multiple digital tools to promote use within the organization, and capable of identifying ways to deploy digital tools to improve personal productivity.
- Highly productive and value oriented.
Advertised until:
Feb. 10, 2025
Are you Qualified for this Role?
Click Here to Tailor Your Resume to Match this Job
Share with Friends!
Similar Internships
Operational Excellence Specialist
Job Title: Operational Excellence Specialist Job Type: Permanent Full-Time Location: Mississauga, O…
Operational Excellence Specialist
Operational Excellence Specialist Reach your career goals with Eirgen Pharma, your future could be …
Operational Excellence Specialist
Job Description Operational Excellence Specialist CIRCLE K EMOBILITY – PROVIDING THE BEST TOT…