Plant General Manager
Posted on May 20, 2025 by US Engineering
- Lawrenceville, United States of America
- $142000.0 - $200000.0
- Full Time
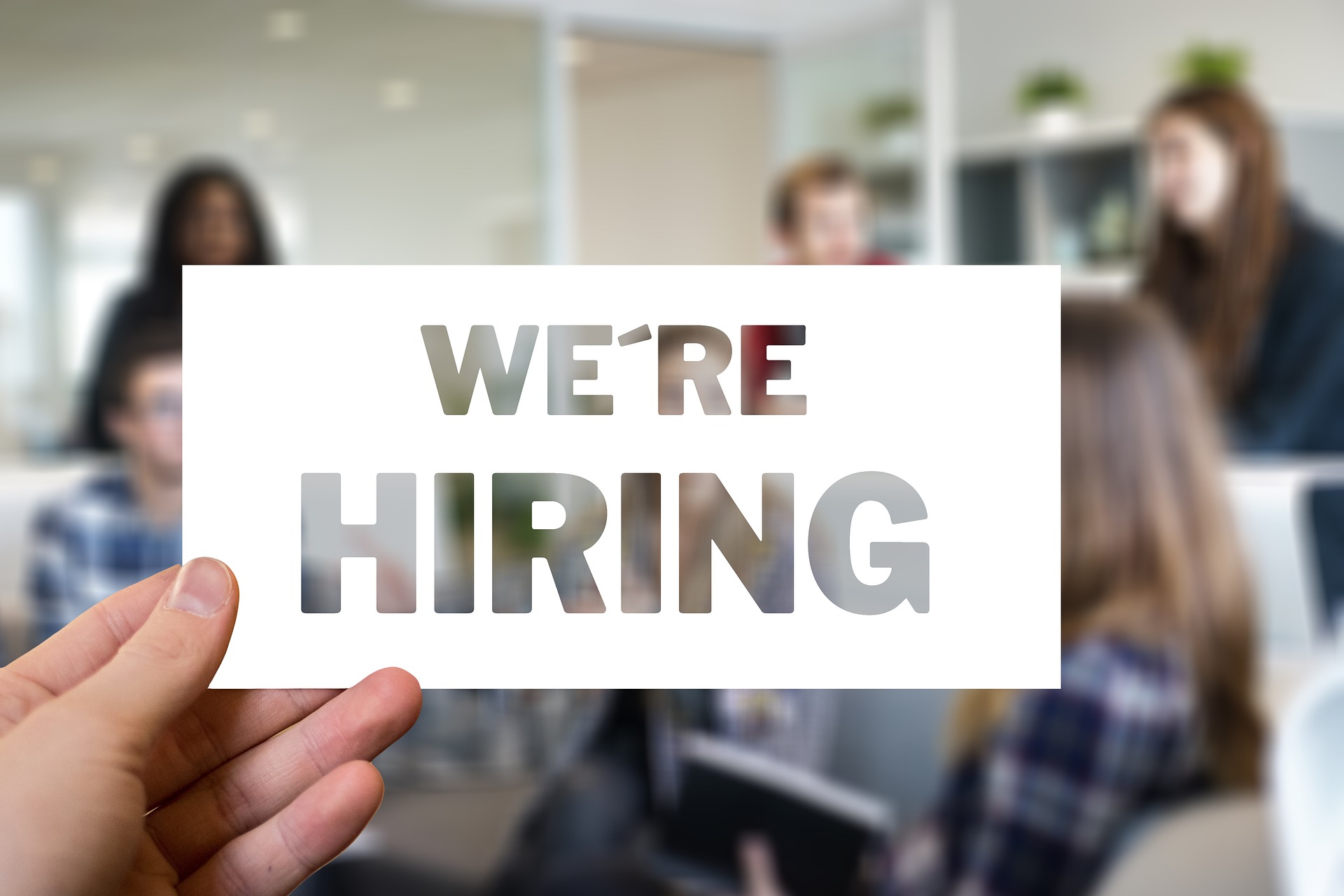
U.S. Engineering has been an industry leader since 1893. How? Constant innovation and a willingness to evolve. The construction industry changes rapidly, and we cultivate a dynamic workplace where even our newest team members can influence change and make an impact. We know that our most valuable asset is our people. Join us!
PLANT GENERAL MANAGER
The Plant General Manager of Metalworks oversees regional plant operations, including safety, quality, productivity, and profitability, fostering an engaging culture and promoting regional alignment and continuous improvement. The General Manager is the overall regional lead for Metalworks, relying on communication through customer relationships, while also having a deep knowledge of each role (leadership and technical requirements) in Metalworks.
Principal Duties and Accountabilities:
Education:
Experience:
Knowledge, skills, and abilities:
Physical and/or Travel demands:
Benefits and Compensation:
This position will be posted until May 30, 2025. To apply, please visit https://www.usengineering.com/careers/job-postings/.
Candidates must be legally authorized to work in the United States on a full-time basis without requiring future sponsorship for employment visa status.
U.S. Engineering is an Equal Employment Opportunity Employer and shall provide equal employment opportunities to all people in all aspects of employer-employee relations, without regard to race, color, creed, national origin, religion, sex, age, sexual orientation, gender identity, disability or veteran status.
U.S. Engineering is compliant with the Drug Free Workplace Act, and all offers of employment are contingent upon the completion of a pre-employment drug screen.
Disclaimer: The above statements are intended to describe the general nature and level of work being performed by people assigned to this position. They are not intended to be construed as an exhaustive list of all responsibilities and job specifications required of employees so classified. U.S. Engineering reserves the right to revise as needed. The job description does not constitute a written or implied contract of employment.
PLANT GENERAL MANAGER
The Plant General Manager of Metalworks oversees regional plant operations, including safety, quality, productivity, and profitability, fostering an engaging culture and promoting regional alignment and continuous improvement. The General Manager is the overall regional lead for Metalworks, relying on communication through customer relationships, while also having a deep knowledge of each role (leadership and technical requirements) in Metalworks.
Principal Duties and Accountabilities:
- Leadership: Lead an engaged team through positive, informed thought while holding others accountable. Eliminate roadblocks and drive processes to result in an environment that team members enjoy contributing to.
- Safety and Quality: Responsible for the safety culture to achieve “zero unsafe behaviors” by partnering with the regional safety/quality managers, trade leadership and Safety Council. Responsible for executing the technical Quality Assurance program by partnering with the Quality Director.
-
Culture: Drive a culture that aligns with USE Company Holdings Cultural Norms, including holding team members accountable while coaching and mentoring.
- Selflessness + Humility
- Care + Trust
- Understanding + Acceptance
- Improvement + Ownership
- Performance: Implements and manages technology/data driven shop processes to achieve productivity and financial goals. Manages a high performance team and effective plant equipment management. Responsible for budgeting, measuring/reporting and financial success.
- Community: Active in internal U.S. Engineering cross company engagements as well as external philanthropic and industry events, including volunteering on advisory boards and finding opportunities for other Metalworks team members.
-
Your week may look like:
- Review of daily win-loss (shop productivity), and deep dive into specific challenges.
- Review backlog of orders (workpacks), understanding those scopes, reviewing estimates and production schedules in order to identify areas of potential risk.
- Planning for work that’s occurring that week, the following week, and the following month. Understanding the forecast and capacity load.
- Working with Manufacturing Engineers to keep new work flowing into the system.
- Working with Mx Project Management to understand customer project characteristics and challenges.
- Working with Trade leadership to assure the regional trade managers are aligned with the sister facility.
- Reviewing and managing regional overhead budgets.
- Review any safety or quality concerns with the respective personnel and follow through accordingly.
- Attend to any emergency safety or security issues.
- Lead shop tours and represent Metalworks.
- Speak at, and lead facility-wide meetings and regional sister company gatherings.
- Own the facility (Trade leads own production equipment), working with Real Estate on building-related issues, utilities, and services.
Education:
- Bachelor’s Degree in Engineering, Construction Science Management, Business administration, or graduation from a certified trade apprenticeship is required.
Experience:
- Experience managing an operations unit within the mechanical construction or manufacturing industry preferred.
- Significant project management experience preferred.
- Certification or significant training in lean manufacturing processes is highly preferred.
Knowledge, skills, and abilities:
- Advanced knowledge of manufacturing process and mechanical construction. This includes project development, estimating, virtual construction, fabrication and site installation for commercial mechanical projects.
- Possesses technical skills for productization of piping and sheetmetal processes.
- Knowledge of industry best practices in construction and manufacturing safety and the ability to foster a culture of efficient execution and safety excellence.
- Business acumen, combined with analytical thinking, resulting in ability to manage company’s opportunities, risk, profitability, volume, etc.
- Proven ability to effectively manage a multitude of operational teams to achieve results, despite multiple and changing priorities. Keeps focused on the goal and possesses the managerial courage to deal with unacceptable situations head on.
- Excellent leadership and communication skills; proven collaborator able to establish and foster effective professional relationships, internally and externally and able to extract maximum efforts/performance from team members.
- Ability to accomplish results through others by leveraging peoples’ strengths, supporting their development, creating clear expectations, setting SMART (Specific, Measurable, Attainable, Relevant, and Time-bound) goals, removing barriers, managing performance and administering accountability.
- Excellent time management skills; operates with a sense of urgency.
- Adaptable and flexible to changing environment.
- Able to effectively manage stress and maintain composure.
Physical and/or Travel demands:
- Work will be done in a combination of environments; including the manufacturing floor, office setting, job sites, etc.
- Requires frequent sitting, standing, walking, keyboarding, use of monitor and telephone. Occasional climbing, reaching, stooping and lifting required.
- Travel requirements: Occasional flights with overnight stays, as well as road travel required to effectively execute the needs of this regional leadership role.
Benefits and Compensation:
- The range for this position has been established at $142,000.00 to $200,000.00 per year and is U.S. Engineering’s good faith and reasonable estimate at the time of the posting. The compensation offered to the finalist selected for this role will be based on a variety of factors, including but not limited to internal equity, experience, education, specialty, and training.
- Your total compensation will go beyond the number on your paycheck. Team members are eligible for a year-end bonus based on company and/or individual performance as well as paid time off. An industry-leading benefits package including health, dental, and vision plans, matching retirement contributions, and matching 529 contributions all add to your bottom line.
This position will be posted until May 30, 2025. To apply, please visit https://www.usengineering.com/careers/job-postings/.
Candidates must be legally authorized to work in the United States on a full-time basis without requiring future sponsorship for employment visa status.
U.S. Engineering is an Equal Employment Opportunity Employer and shall provide equal employment opportunities to all people in all aspects of employer-employee relations, without regard to race, color, creed, national origin, religion, sex, age, sexual orientation, gender identity, disability or veteran status.
U.S. Engineering is compliant with the Drug Free Workplace Act, and all offers of employment are contingent upon the completion of a pre-employment drug screen.
Disclaimer: The above statements are intended to describe the general nature and level of work being performed by people assigned to this position. They are not intended to be construed as an exhaustive list of all responsibilities and job specifications required of employees so classified. U.S. Engineering reserves the right to revise as needed. The job description does not constitute a written or implied contract of employment.
6jodDb0Pvp
Advertised until:
June 19, 2025
Are you Qualified for this Role?
Click Here to Tailor Your Resume to Match this Job
Share with Friends!
Similar Internships
No similar Intern Jobs at the Moment!